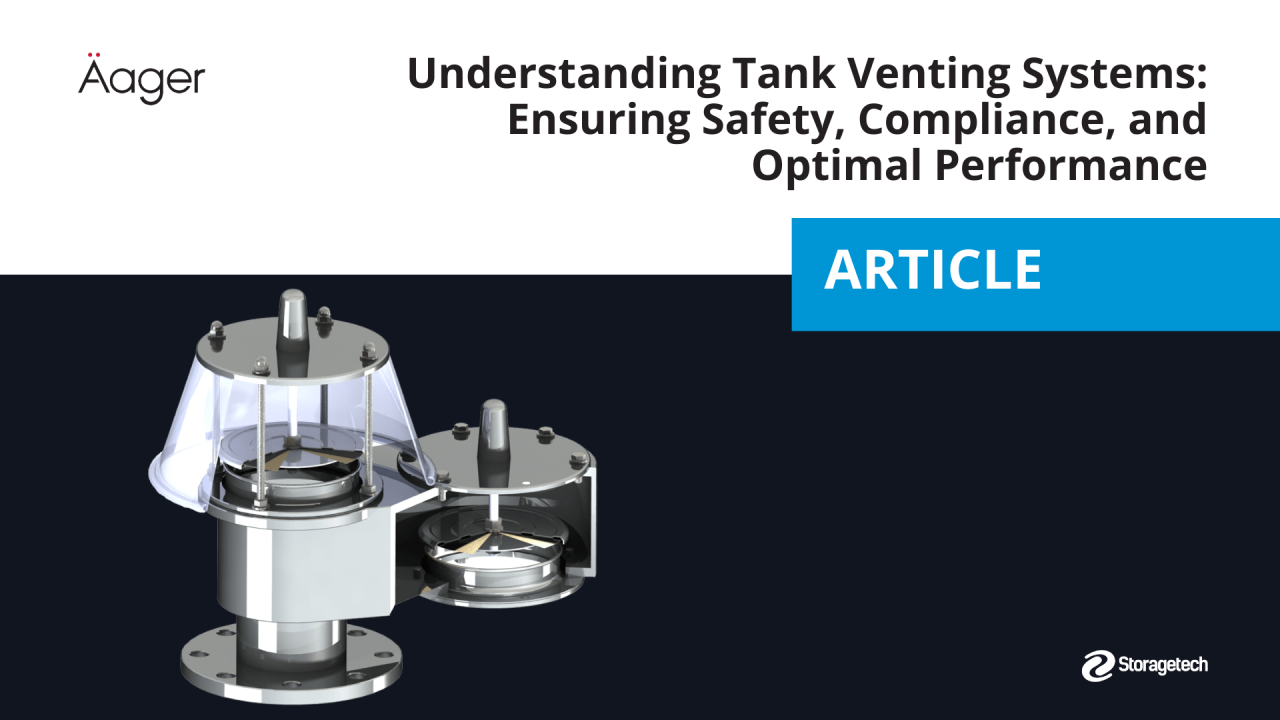
Tank venting systems are critical to the safe and efficient operation of storage tanks across various industries, including oil and gas, chemical processing, and pharmaceuticals. These systems are essential for maintaining tank integrity, preventing overpressure or vacuum conditions, ensuring compliance with environmental regulations, and safeguarding both personnel and assets. This article provides a comprehensive overview of the fundamentals, technical aspects, and advanced considerations of tank venting systems.
The Basics of Tank Venting
A tank venting system facilitates the release of excess pressure or vacuum within a storage tank. As liquids are introduced or removed, or as temperature changes affect the tank’s contents, the internal pressure fluctuates. Without adequate venting, these pressure changes can lead to structural damage, product loss, or catastrophic failure.
Types of Venting Systems
- Open Vents: These are simple and cost-effective solutions that allow free exchange between the tank and the atmosphere. However, they are suitable only for non-hazardous materials due to the lack of containment for harmful vapors.
- Pressure-Vacuum Vents: These bidirectional vents activate at preset pressure or vacuum levels, offering protection against both overpressure and vacuum conditions. They are essential for preventing tank deformation and product contamination.
- Emergency Vents: Designed to handle sudden pressure spikes, emergency vents provide an additional safety layer beyond standard operating vents, particularly in case of fire or other unexpected events.
- Flame Arrestors: Crucial for tanks containing flammable materials, flame arrestors prevent flame propagation into the tank by dissipating the heat from the flame front.
Venting System Design Parameters
Effective vent sizing and design are crucial for the safe operation of storage tanks. The parameters include:
- Volumetric Flow Rate: This is calculated based on the maximum filling or emptying rates and potential vapor generation. Proper flow rate calculation ensures that the vent can handle the tank’s pressure changes without failure.
- Pressure Setting: Contrary to the earlier misconception, pressure settings should be carefully calibrated based on the tank’s Maximum Allowable Working Pressure (MAWP). Typically, the vent is set at a level that provides a safe margin, often around 90% of the MAWP.
- Back Pressure: When designing the vent system, the resistance from downstream piping must be considered to ensure proper operation. Neglecting back pressure can lead to system inefficiencies or malfunctions.
The API Standard 2000 offers detailed guidelines for venting atmospheric and low-pressure storage tanks, including equations for different scenarios to ensure safety and compliance.
Fluid Dynamics in Venting Systems
Understanding the behavior of fluids within venting systems is essential for optimal design:
- Bernoulli’s Principle: This principle is used to analyze the energy balance in a fluid system, particularly in relation to pressure changes. However, it is crucial to apply the Darcy-Weisbach equation for accurate pressure drop calculations across venting pathways.
- Reynolds Number: This dimensionless number determines whether the flow regime is laminar or turbulent, which directly affects the vent’s performance and efficiency.
- Choked Flow: In emergency venting scenarios, when flow velocity reaches sonic levels, it is known as choked flow. This condition is critical in determining the vent size and ensuring the system’s ability to relieve pressure effectively.
Advanced Computational Fluid Dynamics (CFD) modeling is increasingly utilized to simulate complex venting scenarios, optimizing vent placement and sizing for maximum safety and efficiency.
Safety Considerations
The primary function of tank venting systems is to prevent hazardous conditions such as overpressure, which can cause tank rupture, or vacuum conditions, which can lead to tank implosion. Both scenarios present significant risks to personnel, the environment, and the facility. Properly designed, installed, and maintained venting systems mitigate these risks effectively.
Additionally, venting systems play a crucial role in controlling the release of harmful vapors, especially when dealing with volatile organic compounds (VOCs) or other hazardous materials. This ensures both compliance with environmental regulations and protection of the surrounding environment.
Material Selection and Corrosion Mitigation
Selecting the appropriate materials for venting systems is vital for their longevity and performance:
- Stainless Steel (316L, 304): Known for its excellent corrosion resistance, stainless steel is widely used in most applications, particularly in environments with moderate to high corrosion potential.
- Hastelloy: This nickel-based alloy is preferred in highly corrosive environments, such as those with high chloride content, due to its superior corrosion resistance.
- PTFE-lined Vents: For handling highly reactive or corrosive materials, PTFE (Teflon) lining provides chemical inertness and extends the life of the venting system.
Galvanic corrosion must be carefully managed, especially when different metals are in contact. Cathodic protection systems may be necessary for large metallic storage tanks to prevent electrochemical reactions that could compromise the tank’s integrity.
Pressure-Vacuum Vent Valve Mechanics
Modern pressure-vacuum (P/V) vent valves are engineered with precision to ensure reliable operation:
- Pallet Design: Precision-weighted pallets within the valve control the opening pressures, ensuring the vent operates correctly under varying conditions.
- Seat Materials: Seats made from PTFE or FKM (Viton) provide excellent sealing and durability, even in harsh chemical environments.
- Diaphragm Systems: Some P/V vent valves incorporate flexible diaphragms that offer more sensitive pressure control, enhancing the system’s response to pressure changes.
Typical cracking pressures for these valves range from 0.5 to 15 kPa, with flow capacities up to 100,000 m³/h for large tanks, ensuring safety and efficiency in venting operations.
Flame Arrestor Technology
Flame arrestors are indispensable for tanks storing flammable materials:
- Crimped Metal Ribbon: This design offers a large surface area for heat dissipation, effectively extinguishing flames and preventing them from entering the tank.
- Parallel Plate Design: While offering lower pressure drops, this design may be less effective for certain flame types, making it essential to choose the appropriate arrestor based on the specific application.
Flame arrestors must comply with rigorous standards, such as EN ISO 16852 or ATEX directives, to ensure they provide adequate protection against flame propagation.
Compliance and Regulations
Regulatory bodies, such as the Environmental Protection Agency (EPA) and the Occupational Safety and Health Administration (OSHA) in the United States, have established stringent guidelines for tank venting systems. These regulations require regular inspections, proper documentation, and strict adherence to design and operational standards. Non-compliance can result in severe penalties, operational shutdowns, and damage to the company’s reputation.
Vapor Recovery Systems Integration
To meet environmental regulations, vapor recovery systems are often integrated into venting systems:
- Balanced Systems: These systems use the displacement of vapor during filling operations to recover and manage emissions.
- Vacuum-assist Systems: These systems actively capture vapors using pumps, significantly reducing emissions and enhancing environmental compliance.
- Cryogenic Condensation: For valuable or highly volatile products, cryogenic condensation offers an efficient method for vapor recovery, achieving up to 95-99% efficiency.
Innovations in Venting Technology
The field of tank venting continues to evolve with several key innovations:
- Smart Venting Systems: Incorporating sensors and automated controls, these systems optimize venting operations based on real-time conditions, enhancing both safety and efficiency.
- Low-Emission Vents: Designed to minimize VOC emissions, these vents are increasingly important as environmental regulations tighten, helping companies meet stringent standards.
- Corrosion-Resistant Materials: New alloys and coatings are being developed to extend the lifespan of venting systems, particularly in harsh environments where traditional materials may fail.
Smart Venting Technologies
The integration of IoT into tank venting systems is revolutionizing the industry:
- Pressure Transmitters: These devices provide real-time data on tank conditions, allowing for immediate adjustments to venting operations.
- Automated Vent Control: This technology adjusts vent settings automatically based on real-time data, ensuring optimal performance under varying conditions.
- Predictive Maintenance: Using AI algorithms, predictive maintenance systems can foresee potential failures in vent systems, allowing for timely interventions before issues escalate.
These smart systems can be integrated with SCADA networks, enabling remote monitoring and control of venting operations, thus enhancing operational efficiency and safety.
Cryogenic Venting Considerations
For LNG and other cryogenic storage tanks, specialized venting systems are necessary:
- Thermal Cycling: Vents must be designed to withstand the extreme temperature fluctuations that occur in cryogenic environments.
- Material Embrittlement: Special alloys, such as 9% Nickel steel or Invar, are required to prevent embrittlement, which can occur due to the extremely low temperatures.
- Insulation: To prevent ice formation, vacuum-jacketed piping is often used, ensuring that the venting system remains functional in cryogenic conditions.
Properly sized pressure relief systems are essential to manage pressure build-up due to heat ingress, preventing dangerous pressure spikes.
Maintenance and Best Practices
Regular maintenance is essential to ensure the longevity and effectiveness of tank venting systems. This includes:
- Routine Inspections: Regular checks for signs of wear, corrosion, or damage.
- Cleaning: Ensuring vent openings are free from blockages that could impede proper operation.
- Calibration: Regular calibration of pressure settings on pressure-vacuum vents to maintain accuracy.
- Gasket and Seal Replacement: Periodic replacement of gaskets and seals to prevent
Tank venting systems are a critical component of safe and efficient storage operations, representing a complex interplay of fluid dynamics, materials science, and regulatory compliance. As storage requirements become more stringent and diverse, industry professionals must stay informed about the latest technological advancements and design methodologies.
By integrating smart technologies, advanced materials, and sophisticated modeling techniques, modern venting systems can provide unprecedented levels of safety, efficiency, and environmental protection. Whether managing a small chemical storage facility or overseeing a large oil terminal, understanding and implementing proper venting solutions is key to protecting assets, personnel, and the environment.
As the field continues to evolve, ongoing education and adaptation to new technologies and regulations will be essential for those involved in the design, operation, and maintenance of tank venting systems. The future of tank venting lies in smarter, more efficient, and environmentally friendly solutions that can meet the growing demands of industry while ensuring the highest standards of safety and compliance.
Mohammed HASSAN
Technical Coordinator
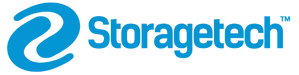