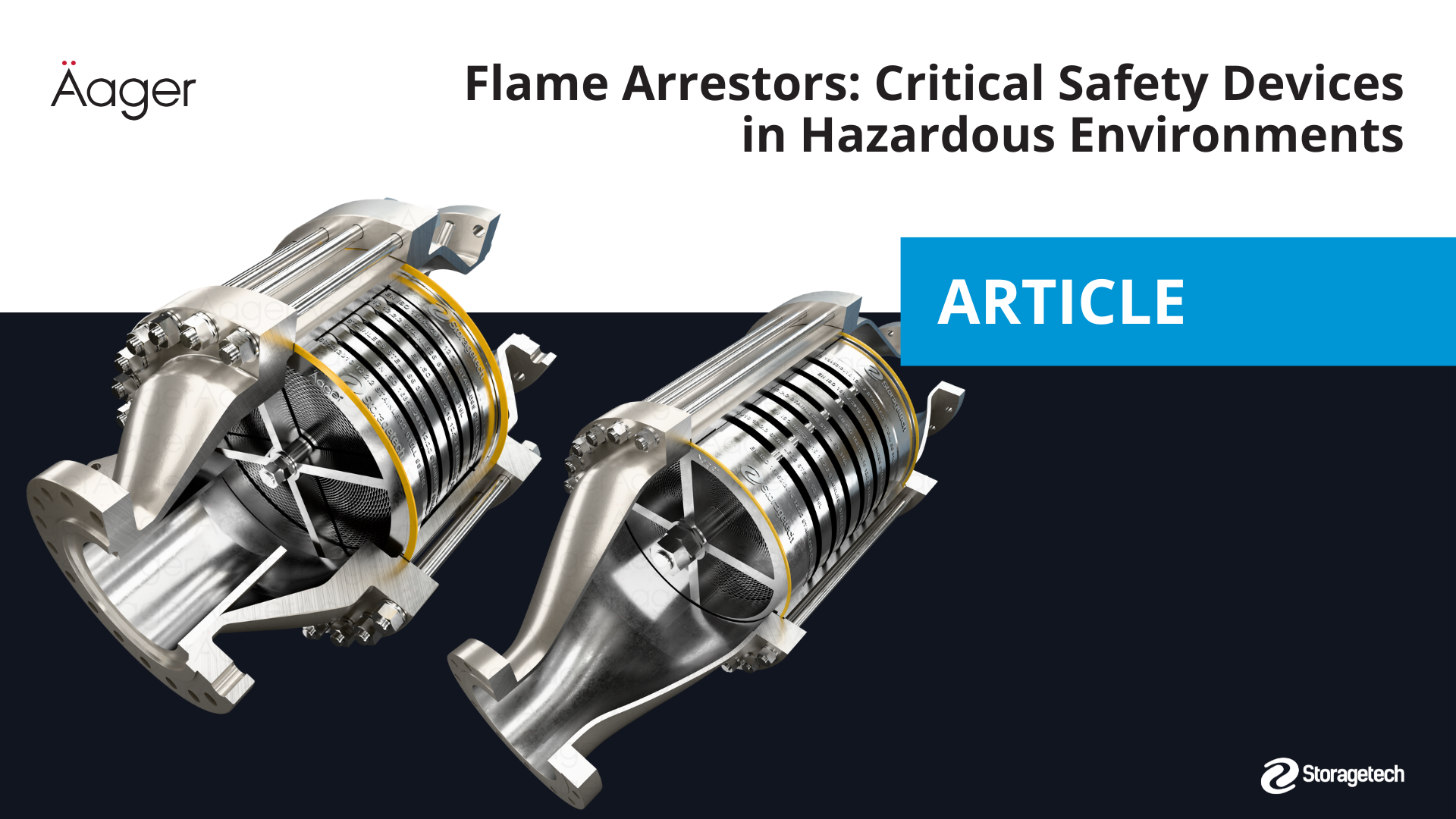
Flame arrestors, also known as flame arresters or detonation arresters, are crucial safety devices designed to prevent the propagation of flames through piping systems, vessels, and equipment in industries where flammable gases or vapors are present.
These devices play a vital role in protecting personnel, equipment, and the environment from the devastating effects of explosions and fires.
This article delves into the technical aspects of flame arrestors, their diverse applications, the critical reasons for their implementation, and essential considerations when selecting and installing these life-saving devices.
1. Principle of Operation
Flame arrestors operate on the principle of quenching a flame front by dissipating its heat. They typically consist of a matrix of small channels or passages that allow gases to flow through under normal conditions. However, when a flame approaches, the arrestor’s design causes the flame front to lose heat to the surrounding metal faster than it can be generated by the combustion process. This heat loss extinguishes the flame, preventing it from propagating further through the system.
The key components of a flame arrestor include:
- a) Housing: Usually made of corrosion-resistant materials like stainless steel or aluminum.
- b) Flame element: The core component, which can be:
- Crimped metal ribbon
- Perforated plates
- Packed beds of small diameter tubes or beads
- c) End connections: Flanged, threaded, or welded, depending on the application.
- d) Pressure relief mechanism: In some designs, to prevent damage from pressure buildup.
2. Types of Flame Arrestors
2.1 End-of-Line Flame Arrestors These are installed at the open end of a pipe or vent, protecting against external ignition sources. They are commonly used on storage tank vents, flare systems, and exhaust pipes.
2.2 In-Line Flame Arrestors Placed within piping systems, these arrestors protect against flame propagation in both directions. They are crucial in process pipelines, fuel supply lines, and vapor recovery systems.
2.3 Detonation Flame Arrestors Designed to withstand and quench high-speed flame fronts (detonations), these robust arrestors are used in high-risk applications where deflagration can transition to detonation.
2.4 Hydraulic Flame Arrestors These use a liquid seal to prevent flame propagation and are often employed in biogas plants and sewage treatment facilities.
For our flame arrestor products visit: https://storagetech.de/flame-arrestors/
3. Applications and Reasons for Use
3.1 Oil and Gas Industry
- Storage Tanks: Flame arrestors are installed on tank vents to prevent external ignition sources from causing tank explosions.
- Reason: Hydrocarbon vapors in storage tanks can form explosive mixtures with air. Flame arrestors protect against lightning strikes, static electricity, or other ignition sources.
- Flare Systems: Arrestors are used to prevent flashback from the flare tip into the flare header.
- Reason: Flare systems handle large volumes of flammable gases. Flame arrestors prevent the flame from traveling back into the process plant, which could lead to catastrophic explosions.
- Vapor Recovery Units (VRUs): In-line arrestors protect VRUs from potential ignitions in loading operations.
- Reason: VRUs collect and process volatile organic compounds (VOCs). Flame arrestors prevent any ignition at loading points from propagating into the VRU system.
3.2 Chemical Processing Industry
- Reactor Vent Lines: Flame arrestors are installed to protect reactors from external ignition sources.
- Reason: Many chemical reactions produce flammable gases. Arrestors prevent flames from entering reactors through vent lines, which could cause runaway reactions.
- Solvent Recovery Systems: In-line arrestors are used in solvent distillation and recovery processes.
- Reason: Solvents are often highly flammable. Flame arrestors prevent fire propagation between different parts of the recovery system.
3.3 Pharmaceutical Industry
- Batch Reactors: Flame arrestors protect against flame propagation in reactor vent systems.
- Reason: Pharmaceutical processes often involve flammable solvents and gases. Arrestors prevent flames from spreading through interconnected reactor systems.
3.4 Biogas and Wastewater Treatment
- Anaerobic Digesters: Flame arrestors are installed on biogas lines and vents.
- Reason: Biogas is highly flammable. Arrestors prevent flame propagation that could damage digesters and associated equipment.
3.5 Paint and Coating Industry
- Spray Booths: Flame arrestors are used in ventilation systems of spray painting booths.
- Reason: Paint vapors are highly flammable. Arrestors prevent fires in the booth from spreading to the central ventilation system.
3.6 Transportation
- Fuel Tankers: Flame arrestors are installed on tanker vents and filling lines.
- Reason: Fuel vapors are extremely flammable. Arrestors prevent external ignition sources from causing explosions during transport and loading/unloading operations.
4. Critical Reasons for Using Flame Arrestors
4.1 Personnel Safety Flame arrestors are primarily installed to protect human life. By preventing flame propagation, they significantly reduce the risk of explosions and fires that could cause severe injuries or fatalities.
4.2 Equipment Protection Explosions and fires can cause catastrophic damage to industrial equipment. Flame arrestors protect valuable assets, preventing costly damage and prolonged downtime.
4.3 Environmental Protection By preventing large-scale fires and explosions, flame arrestors help avoid the release of hazardous materials into the environment, protecting ecosystems and preventing pollution.
4.4 Regulatory Compliance Many industries are required by law to implement flame arrestors as part of their safety systems. Compliance with these regulations is crucial for legal operation and insurance purposes.
4.5 Process Continuity Flame arrestors allow for the safe venting of gases and vapors during normal operations while providing protection against abnormal events, ensuring continuous and safe process operation.
4.6 Risk Mitigation As part of a comprehensive safety system, flame arrestors help reduce overall plant risk, which can lead to lower insurance premiums and improved stakeholder confidence.
5. Selecting the Right Flame Arrestor
When choosing a flame arrestor, several critical factors must be considered to ensure optimal performance and safety:
5.1 Process Conditions
- Gas/Vapor Composition: The specific flammable substances in the system will determine the required flame arrestor specifications.
- Temperature Range: Ensure the arrestor can withstand both the normal and maximum process temperatures.
- Pressure Conditions: Consider both normal operating pressure and potential pressure spikes.
- Flow Rate: The arrestor must accommodate the system’s maximum flow rate without excessive pressure drop.
5.2 Installation Location
- End-of-Line vs. In-Line: Determine whether the arrestor will be at a pipe terminus or within the piping system.
- Outdoor vs. Indoor: Environmental factors like rain, snow, or dust may necessitate additional protection for the arrestor.
5.3 Potential Ignition Scenarios
- Deflagration vs. Detonation: Assess the risk of high-speed detonations, which require more robust arrestor designs.
- Endurance Burning: Consider whether prolonged flame impingement is possible, requiring arrestors with specific endurance burn ratings.
5.4 Material Compatibility
- Corrosion Resistance: Ensure the arrestor materials are compatible with the process fluids and environmental conditions.
- Temperature Resistance: Verify that all components can withstand both normal and upset temperature conditions.
5.5 Certification and Standards
- Regulatory Compliance: Choose arrestors that meet or exceed relevant industry standards (e.g., EN ISO 16852, ATEX Directive 2014/34/EU).
- Third-Party Certification: Look for arrestors tested and certified by recognized bodies like FM Global or UL.
5.6 Maintenance Requirements
- Ease of Inspection: Consider designs that allow for easy visual inspection and cleaning.
- Replacement Parts: Ensure the availability of spare parts and ease of element replacement.
5.7 Pressure Drop
- System Impact: Evaluate the arrestor’s effect on system pressure drop and ensure it doesn’t negatively impact process efficiency.
5.8 Size and Weight
- Space Constraints: Consider available space for installation and ensure proper support structures are in place.
5.9 Cost Considerations
- Initial Cost vs. Lifecycle Cost: While initial cost is important, also consider long-term factors like maintenance requirements and expected lifespan.
For our flame arrestor products visit: https://storagetech.de/flame-arrestors/
6. Installation and Maintenance Best Practices
6.1 Proper Installation
- Follow manufacturer guidelines for orientation and positioning.
- Ensure proper support to prevent stress on connecting pipework.
- Use appropriate gaskets and fasteners for the service conditions.
6.2 Regular Inspection
- Implement a routine inspection schedule based on service conditions and manufacturer recommendations.
- Check for signs of corrosion, fouling, or physical damage.
6.3 Cleaning and Maintenance
- Clean arrestor elements according to manufacturer instructions, typically using solvents or ultrasonic cleaning methods.
- Replace damaged or degraded components promptly.
6.4 Documentation
- Maintain detailed records of inspections, maintenance activities, and any incidents.
- Keep certificates of conformity and performance data readily accessible.
Flame arrestors are indispensable safety devices in industries dealing with flammable gases and vapors. Their proper selection, installation, and maintenance are crucial for ensuring the safety of personnel, protection of valuable assets, and compliance with regulatory requirements. As industries continue to evolve and face new challenges, the importance of flame arrestors in comprehensive safety strategies remains paramount. By understanding the technical aspects and critical considerations outlined in this article, engineers and safety professionals can make informed decisions to implement these life-saving devices effectively, contributing to safer and more resilient industrial operations.
Mohammed HASSAN
Technical Coordinator
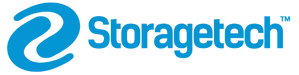