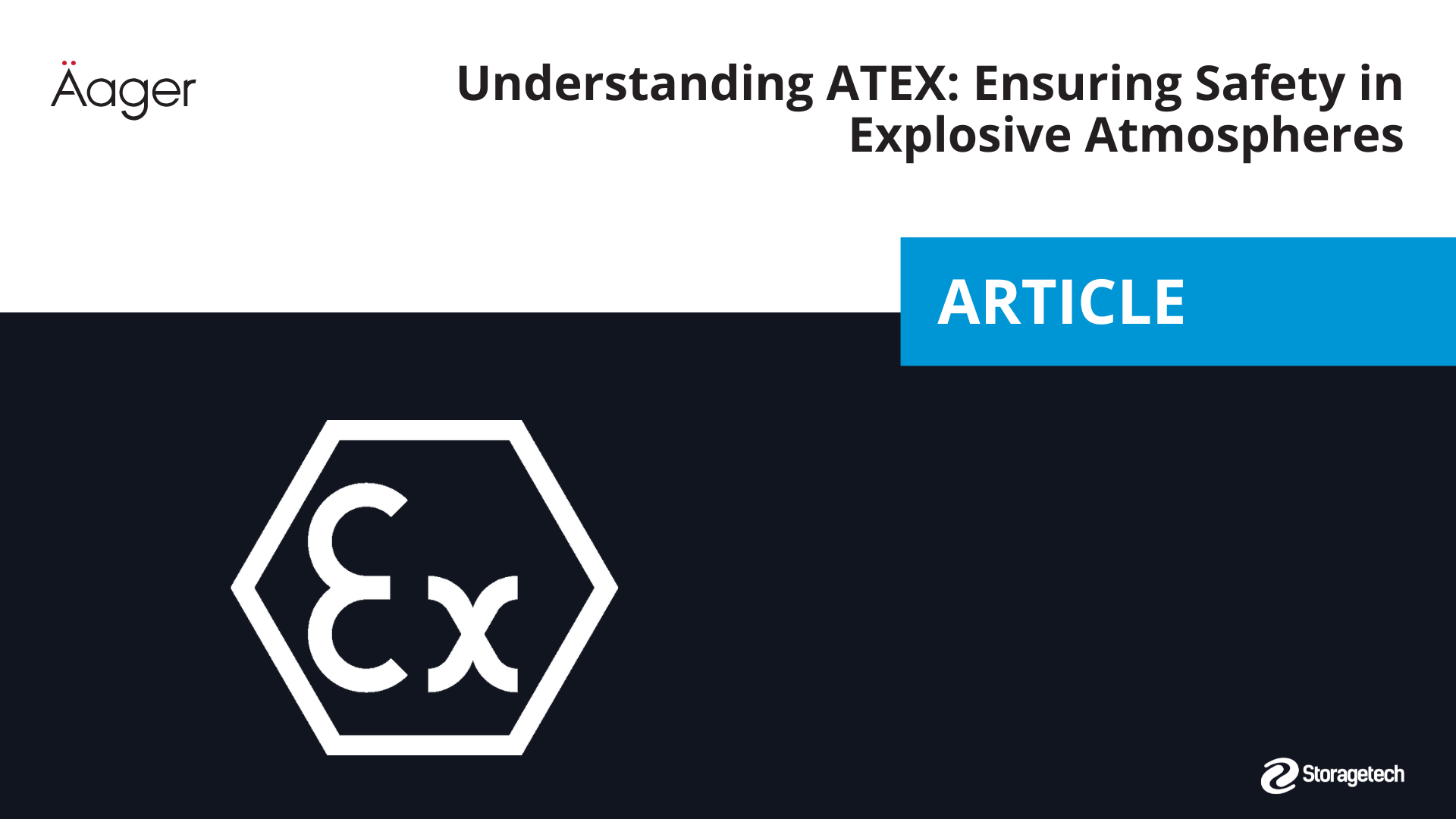
ATEX, derived from the French “Atmosphères Explosibles,” refers to two European Union directives that regulate equipment and work environments that are prone to explosive atmospheres. These directives ensure that products used in hazardous areas, where there is a risk of explosion due to the presence of flammable gases, vapors, or dust, meet the essential health and safety requirements. For engineers and professionals working in industries such as oil and gas, chemical processing, and food manufacturing, understanding ATEX is crucial to ensuring safety and compliance.
The Importance of ATEX Compliance
Explosive atmospheres can arise in various industrial settings, particularly where flammable substances are processed or stored. The risk of explosion is not limited to obvious sources like oil and gas; even dust from materials like grain, sugar, or metal can create hazardous conditions. ATEX compliance is critical for preventing accidents that could result in significant damage, injury, or loss of life.
Directive 2014/34/EU: This directive governs the equipment and protective systems intended for use in potentially explosive atmospheres. It covers a broad range of products, including motors, switches, and sensors, which must be designed and tested to prevent ignition.
Directive 1999/92/EC: This directive focuses on the safety of workers in explosive atmospheres. It mandates that employers assess risks, classify hazardous areas into zones, and implement appropriate safety measures.
ATEX Zoning and Classification
One of the key concepts in ATEX is the classification of hazardous areas into zones based on the frequency and duration of the presence of an explosive atmosphere:
- Zone 0: An area where an explosive atmosphere is present continuously or for long periods.
- Zone 1: An area where an explosive atmosphere is likely to occur in normal operation.
- Zone 2: An area where an explosive atmosphere is not likely to occur in normal operation but may occur for short periods.
For dust, the zones are similar but labeled as Zone 20, Zone 21, and Zone 22.
The correct classification of these zones is essential for selecting the appropriate equipment and safety measures. Engineers must assess the likelihood of explosive atmospheres and select equipment certified for the correct ATEX zone to prevent ignition sources from causing an explosion.
Technical Aspects of ATEX-Certified Equipment
ATEX-certified equipment is designed with various safety features to prevent ignition:
- Intrinsic Safety (IS): This design principle limits the electrical and thermal energy available in the equipment to levels that cannot ignite the surrounding atmosphere. IS is often used in instrumentation and control devices.
- Explosion-Proof (Ex d): Equipment is housed in an enclosure that can withstand an explosion within it and prevent the transmission of the explosion to the surrounding atmosphere. This method is common in motors and switchgear.
- Increased Safety (Ex e): This technique enhances the safety of electrical components by preventing the formation of sparks, arcs, or hot surfaces during normal operation.
Engineers should be familiar with these protection concepts to make informed decisions when designing systems for hazardous areas. The choice of equipment depends on the zone classification and the specific characteristics of the explosive atmosphere, such as the type of gas or dust and its temperature.
The Role of Storagetech in ATEX Compliance
Storagetech, specializes in the design and manufacturing of storage tank safety and emission control equipment that meets ATEX standards. Storagetech products, such as pressure vacuum valves, flame arrestors, and floating suction systems, are engineered to prevent the formation of explosive atmospheres or to mitigate their effects.
- Flame Arrestors: These devices prevent flames from traveling back into the tank, thereby preventing potential explosions. Storagetech flame arrestors are designed according to ATEX requirements, ensuring that they perform effectively in hazardous environments.
- Pressure Vacuum Valves (PVRVs): PVRVs maintain tank pressure within safe limits, reducing the risk of overpressure and vacuum conditions that could lead to a tank rupture or explosion.
- Floating Roofs and Seals: These components minimize the release of flammable vapors, reducing the risk of forming an explosive atmosphere above the stored liquid.
Challenges in ATEX Implementation
While ATEX provides a clear framework for safety, implementation can be complex. Challenges include:
- Accurate Zone Classification: Misclassification of hazardous areas can lead to the use of inappropriate equipment, increasing the risk of explosion.
- Maintaining Equipment Integrity: Regular maintenance is essential to ensure that ATEX-certified equipment continues to function safely. For example, seals may degrade over time, leading to potential leaks of flammable gases.
- Integration with Non-ATEX Systems: Engineers often face challenges when integrating ATEX-certified equipment with non-ATEX systems. This requires careful design and thorough testing to ensure compatibility and safety.
ATEX is a vital aspect of safety in industries where explosive atmospheres are a risk. For engineers, understanding the technical aspects of ATEX, from zoning and classification to the design principles of certified equipment, is crucial for ensuring both safety and compliance. Storagetech’s range of ATEX-certified products provides reliable solutions for managing the risks associated with explosive atmospheres, helping industries maintain safe and efficient operations.
By staying informed about the latest ATEX standards and technologies, engineers can design systems that protect both personnel and assets, ensuring that operations are not only efficient but also safe from the dangers of explosive atmospheres.
Mohammed HASSAN
Technical Coordinator
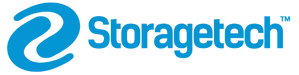