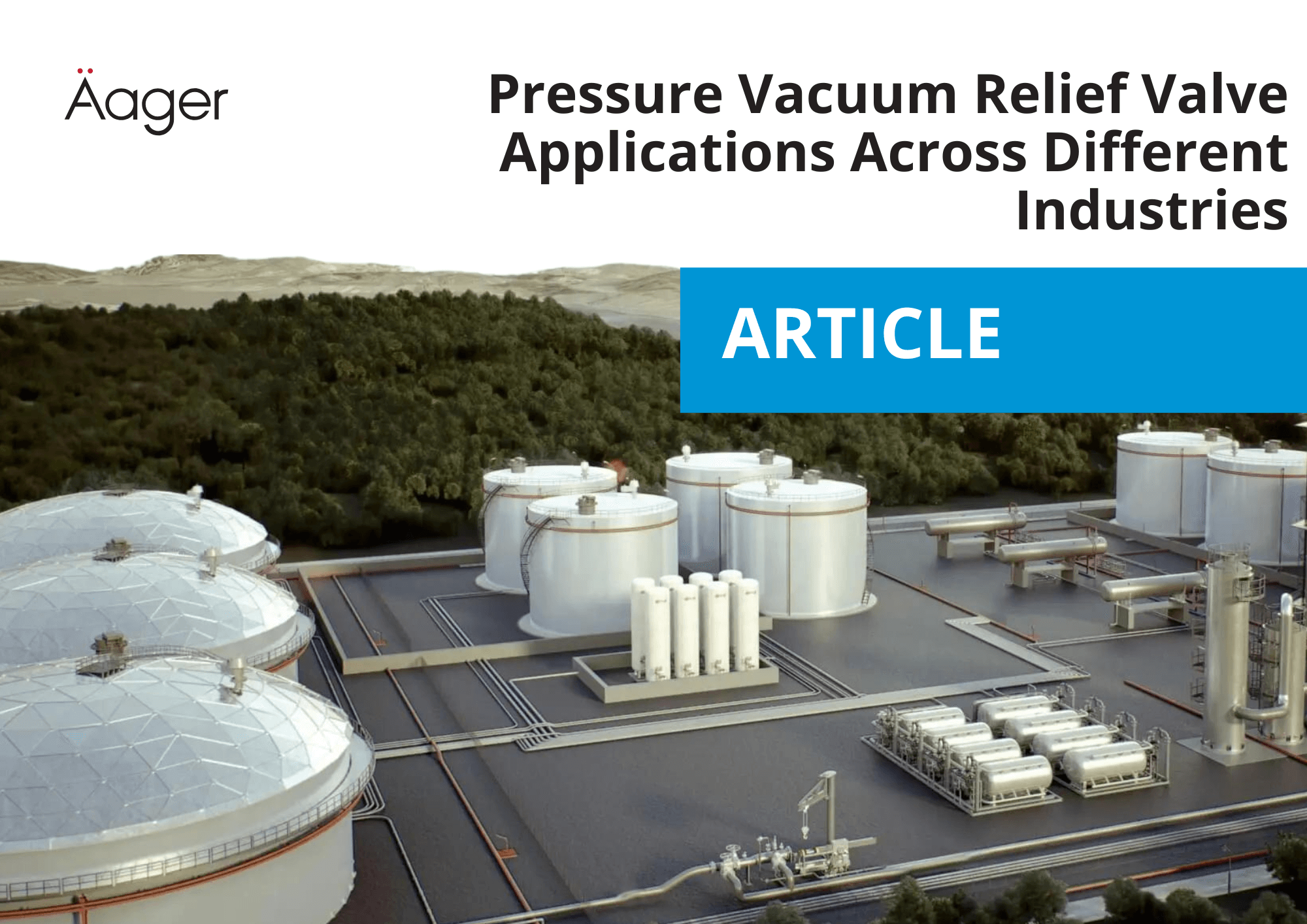
Across multiple sectors, maintaining safe and efficient operations often hinges on the proper management of tank pressures. Pressure Vacuum Relief Valves (PVRVs) are central to this effort, acting as safeguards against overpressure or excessive vacuum conditions in storage tanks and process vessels. While these specialized valves are popular in oil and gas, their versatility makes them indispensable in a wide range of other industries—including biotechnology, pharmaceuticals, food processing, and beyond. Below, we explore how PVRVs deliver value in diverse settings, emphasizing both safety and operational effectiveness.
1. Biotechnology: Safeguarding Sensitive Cultures and Processes
Protecting Sterile Environments
In the biotechnology sector, storage and fermentation vessels often contain sensitive microbial cultures or high-value biologics. Even small variations in pressure can compromise sterility, jeopardizing entire batches of product. PVRVs come into play by maintaining a consistent internal environment. When pressure spikes—due to off-gassing during fermentation, for example—the valve releases excess pressure, preventing damage to the vessel or contamination from forced leaks.
Keeping Energy Costs in Check
Biotech processes sometimes require specific temperature and aeration conditions. If a vessel’s pressure is not managed properly, more energy might be needed for heating, cooling, or sterilization. PVRVs, by allowing only the necessary exchange of gases, help maintain the right balance, minimizing unnecessary energy consumption.
Regulatory Compliance
Biotech facilities operate under stringent quality and safety standards, such as cGMP (Current Good Manufacturing Practice) in the pharmaceutical realm. A reliable Pressure Vacuum Relief Valve helps plants meet these requirements by ensuring traceable control of tank pressures, thus preserving both product quality and compliance.
2. Food and Beverage: Preserving Product Integrity and Flavors
Controlled Fermentation
Industries like brewing, winemaking, and dairy rely heavily on fermentation processes. Too much pressure or vacuum can alter flavor profiles or cause product losses. By automatically venting excess CO₂ or allowing air intake when vacuum conditions arise, PVRVs protect the consistency and taste of food and beverage products.
Odor and Emission Control
Food processing tanks often store substances that can produce strong odors, particularly in rendering plants or facilities handling spices and herbs. PVRVs help manage these odors and emissions by sealing tanks when the internal pressure is within normal limits. This protects surrounding communities from unpleasant smells and helps meet environmental regulations.
3. Pharmaceuticals: Ensuring Purity and Compliance
Protecting High-Value Chemicals
Pharmaceutical facilities handle a vast range of costly chemicals, active pharmaceutical ingredients (APIs), and solvents. Whether these substances are kept in stainless steel reactors or small-scale lab tanks, they often require precise pressure control to maintain purity and efficacy. A properly calibrated PVRV prevents external contaminants from entering and reduces vapor leaks that could result in monetary losses or safety hazards.
Documentation and Validation
Pharmaceuticals are subject to rigorous documentation standards, including validation protocols for process equipment. Pressure Vacuum Relief Valves are no exception. Their set points, calibration records, and maintenance logs must be kept meticulously. Modern facilities often incorporate digital monitoring to track PVRV performance, integrating data directly into enterprise resource planning (ERP) systems for streamlined compliance reporting.
4. Chemicals and Specialty Gases: Controlling Volatility
Handling Reactive Substances
Chemical plants frequently store highly reactive substances that can generate significant vapor pressure—especially under temperature variations or mixing operations. A well-selected PVRV not only shields tanks from ruptures but also prevents backflow of air that could trigger exothermic reactions. By serving as the first line of defense, these valves reduce the likelihood of chain reactions that may jeopardize staff safety and damage equipment.
Minimizing Emissions and Product Loss
In an era of tightening environmental regulations, chemical producers are under pressure to cut emissions. Uncontrolled tank venting contributes to volatile organic compound (VOC) emissions and potential chemical releases. PVRVs, by maintaining a tight seal until pressures reach safe relief points, curb these emissions significantly—aligning with EPA or local environmental authority guidelines.
5. Petrochemicals and Fuel Storage: Safety Under High Volumes
Large-Scale Tanks and Extreme Conditions
Few industries handle quantities of liquid on the scale seen in fuel storage terminals and refineries. Tanks can hold thousands—or even millions—of liters of crude oil, gasoline, or other refined products. Here, a Pressure Vacuum Relief Valve is critical: a sudden overpressure event can cause catastrophic tank ruptures, while vacuum conditions may lead to wall collapses. By maintaining an optimal pressure differential, PVRVs help avert potentially deadly accidents and significant product losses.
Energy and Cost Efficiency
In fuel storage, excessive evaporation represents both an environmental hazard and a financial burden. PVRVs prevent evaporation losses by only venting when tank pressures exceed set parameters—thus curbing the escape of volatile fuels. This also helps satisfy environmental regulations around hydrocarbon emissions and lessens the need for costly vapor recovery units.
6. PVRV Selection Criteria for Different Sectors
Pressure and Temperature Range
From low-temperature biotech processes to high-temperature chemical distillation, each sector presents unique operating pressure and temperature conditions. Plant operators must select PVRVs rated for the specific extremes—avoiding devices that might malfunction under demanding circumstances.
Material Compatibility
Corrosive chemicals, active enzymes, or hydrocarbon vapors can degrade certain metals over time. In industries like pharmaceuticals and biotechnology, stainless steel PVRVs are common due to their resistance to corrosion and ease of cleaning. Meanwhile, the petrochemical field may require specialized alloys or coatings to handle acidic or sulfur-laden substances.
Maintenance Protocols
Whether in a food-processing plant or a large-scale fuel terminal, regular inspections and calibrations ensure that PVRVs continue to deliver reliable performance. Adhering to a planned schedule—aligned with industry best practices—helps identify wear, tear, or corrosion early and prevents unexpected outages.
Final Thoughts on Multi-Industry Applications
Pressure Vacuum Relief Valves (PVRVs) have become a mainstay in numerous industries for a reason: they serve as a crucial line of defense against mechanical failures, product losses, and safety hazards. From fermentation tanks in biotech labs to massive fuel storage fields, these valves adapt to a variety of environments, each posing its own challenges and demands.
The overarching advantage lies in their self-regulating nature—opening or closing as needed to preserve structural integrity, product quality, and staff safety. When chosen and maintained correctly, PVRVs can enhance operational efficiency, ensure compliance with stringent regulations, and minimize environmental impacts.
For any operation involving volatile or sensitive materials, integrating the right PVRV into the tank’s design is a best practice that extends equipment life, safeguards personnel, and ultimately supports long-term, sustainable growth across multiple industrial sectors.
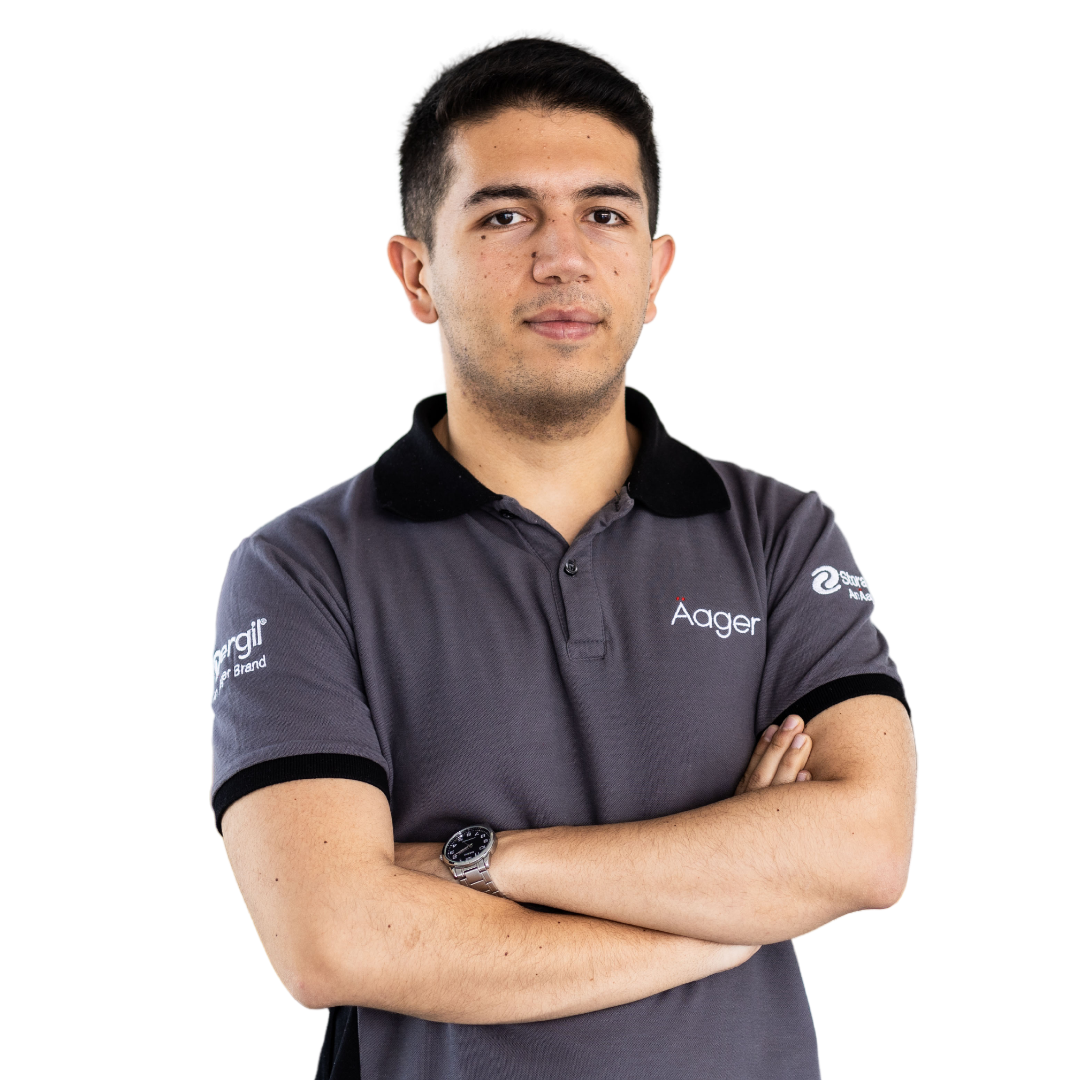
Barış KARAKUZULU
Sales Engineer
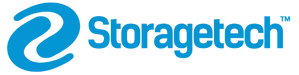