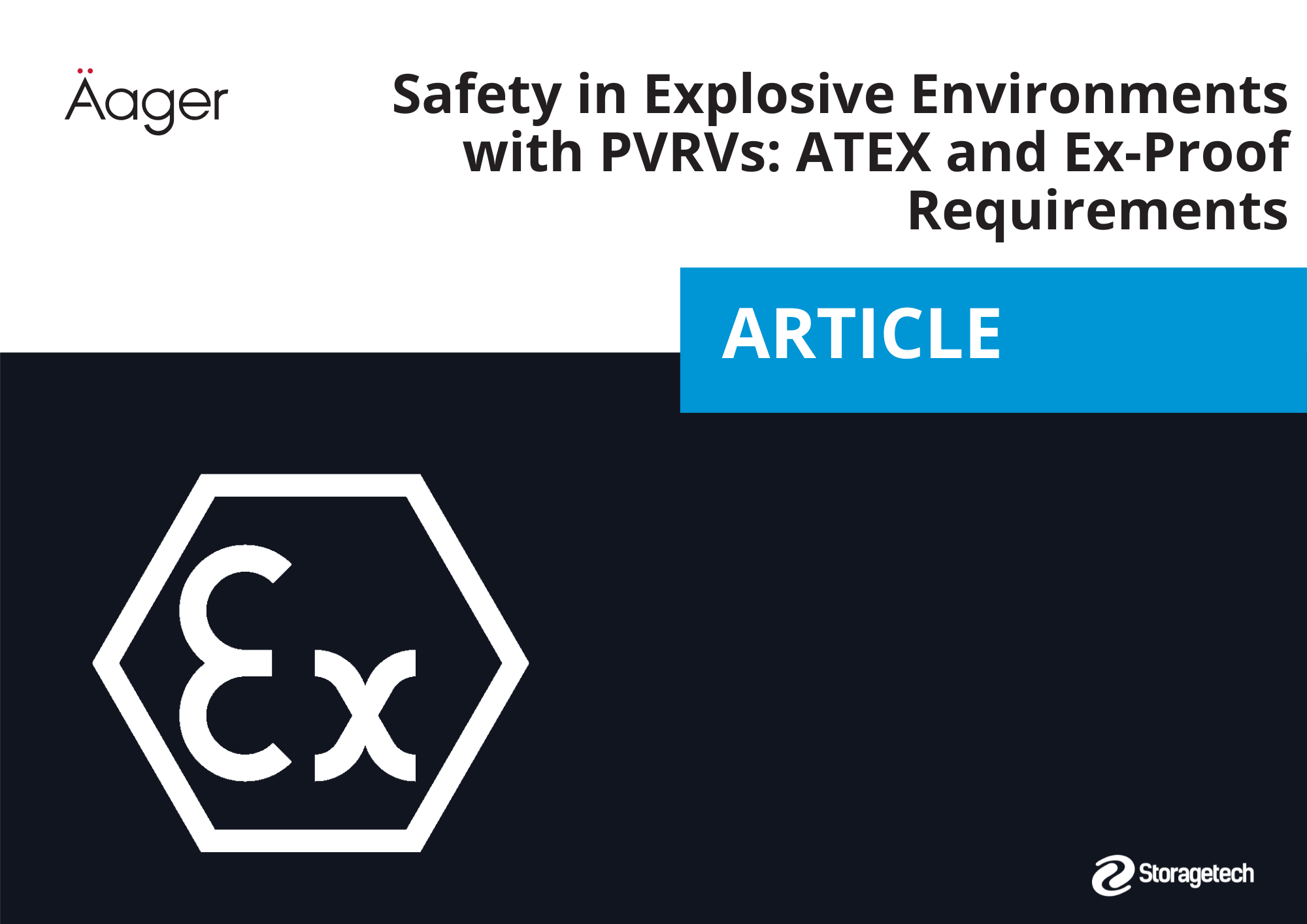
Storage tanks and process vessels that handle flammable or potentially explosive substances demand strict compliance with safety standards. Pressure Vacuum Relief Valves (PVRVs), often called breather valves, serve as a critical line of defense by controlling internal tank pressures. Yet, in explosive atmospheres, standard PVRVs may not suffice. Facilities must ensure that these valves meet ATEX guidelines and explosion-proof (Ex-proof) requirements to prevent ignition risks. Below, we explore the core principles of operating PVRVs in explosive environments and how ATEX and Ex-proof regulations come into play.
1. Understanding Explosive Atmospheres and PVRVs
Defining Explosive Atmospheres
An explosive atmosphere arises when a mixture of air and flammable gases, vapors, or dusts can combust under certain conditions. Even a minor spark or heat source can ignite these mixtures, leading to fires or blasts with severe implications for plant operations and personnel safety. In many industries—such as oil and gas, chemicals, and pharmaceuticals—stored materials can easily produce such environments.
Role of PVRVs in Hazardous Areas
Pressure Vacuum Relief Valves help maintain safe tank pressures by venting out excess gas (pressure relief) or allowing air in (vacuum relief). In standard operations, this functionality helps avoid overpressure or vacuum conditions that could damage tank walls. However, in hazardous zones, the valve itself must not become an ignition source. Proper ATEX classification and Ex-proof design ensure that the PVRV won’t trigger a spark or release enough heat to ignite an explosive atmosphere.
2. Key Regulatory Frameworks: ATEX and Ex-Proof
ATEX Directives
ATEX (derived from the French term “Atmosphères Explosibles”) is the European regulatory framework for equipment used in potentially explosive environments. It includes two key directives:
- ATEX 2014/34/EU (Equipment Directive)
Covers design, testing, and certification requirements for equipment used in explosive atmospheres. PVRVs that fall under ATEX must be tested to prove they won’t ignite flammable gases or vapors. - ATEX 99/92/EC (Workplace Directive)
Focuses on protecting workers, outlining how employers must classify hazardous areas and select suitable equipment.
Ex-Proof Standards
In addition to ATEX directives, the term Ex-proof (explosion-proof) often appears in international contexts. Different regions use varying standards—like IECEx or NEC in North America—to govern the design of explosion-proof electrical and mechanical equipment. For PVRVs, being “Ex-proof” typically means:
- The device is robustly built to prevent sparks, arcs, or hot surfaces in normal and certain fault conditions.
- It meets specific testing criteria related to its temperature class, gas group, and protection mode (e.g., flameproof, intrinsic safety, or non-sparking, depending on the application).
3. Design Considerations for PVRVs in Explosive Environments
Material Selection
Valves in ATEX/Ex-proof setups must use materials that resist corrosion and do not produce friction-based sparks. Common choices include stainless steel and specialized alloys. The seal materials (O-rings, gaskets) must also withstand chemicals and high temperatures without degrading.
Temperature Class and Gas Group
Each explosive atmosphere is categorized by gas groups (I, IIA, IIB, IIC, etc.) and temperature classes (T1–T6). PVRVs intended for these environments must carry the correct certification, ensuring they can handle:
- Gas Group: Indicates the type of gas or vapor. Group IIC, for instance, covers hydrogen—one of the most challenging gases due to its high flammability.
- Temperature Class: Reflects the maximum surface temperature of the equipment. A PVRV rated for T3 (200 °C) must not exceed that surface temperature under normal or fault conditions.
Spark Prevention and Static Discharge
In explosive atmospheres, electrostatic sparks or mechanical impacts can initiate combustion. Ex-proof PVRVs often include design elements such as:
- Grounding or Bonding Points: To safely dissipate static charges.
- Non-sparking Materials: Metals that do not easily produce sparks upon contact.
- Smooth Internal Surfaces: Minimizing internal friction or abrasive contact that could generate heat.
4. Compliance and Certification Testing
Type Approval and Marking
ATEX-compliant PVRVs will display specific markings, typically including:
- CE Mark: Confirms conformance to European directives, including ATEX.
- Ex Symbol: Denotes suitability for use in explosive atmospheres.
- Equipment Category: Reflects the zone classification where the valve is intended to operate (Zone 0, 1, or 2 for gases).
- Gas Group and Temperature Class: Identifies the exact range of conditions for safe operation.
Performance Validation
Independent testing bodies—often referred to as Notified Bodies—conduct rigorous explosion testing on PVRV designs to confirm they meet the ATEX standards. These tests might involve:
- Flame Endurance Tests: Ensuring the valve can withstand exposure to a controlled flame without igniting the internal process media.
- Operational Tests: Verifying that the valve responds correctly (opens and closes) at designated pressure set points under explosive-risk conditions.
- Temperature Rise Assessments: Measuring the valve’s surface temperature during extended operations.
5. Installation and Maintenance Best Practices
Hazardous Area Classification
Before installing an ATEX-certified PVRV, facility owners should carry out a hazardous area classification to identify zones where explosive atmospheres can form. Selecting the right category of valve (e.g., Category 1 for Zone 0) ensures compliance and safety.
Proper Mounting and Orientation
For optimal performance, follow manufacturer guidelines regarding the mounting position, orientation (vertical or angled), and torque values for flange connections. Some models have built-in flame arrestors or specific vent screens, which require correct alignment to function effectively.
Routine Inspection and Calibration
Even the best-designed Ex-proof PVRV can fail if neglected. Common maintenance steps include:
- Visual Inspections: Check for signs of corrosion, wear, or loose fasteners.
- Leak Testing: Confirm the valve seals properly under nominal pressure conditions.
- Calibration: Ensure set points for opening and closing remain accurate—slight deviations could compromise both safety and compliance.
- Documentation: Keep detailed logs of maintenance actions, replacements, and test results for audit and traceability purposes.
6. Achieving a Safer Operating Environment
For sites handling flammable gases, liquids, or dusts, Pressure Vacuum Relief Valves are more than just a safeguard against tank damage—they also serve as a frontline measure against explosions. By aligning with ATEX directives and Ex-proof standards, operators can:
- Prevent Ignition Sources
- A properly rated PVRV won’t spark or overheat, even under demanding process conditions.
- Enhance Regulatory Compliance
- Meeting local and international guidelines helps avoid fines, shutdowns, and liability issues.
- Boost Stakeholder Confidence
- Demonstrating advanced risk management instills trust among employees, regulators, and community members.
Balancing Safety and Efficiency
Ensuring PVRVs meet ATEX and Ex-proof requirements might seem complex, but the benefits are substantial. Apart from safeguarding workers and infrastructure, explosion-proof PVRVs maintain the internal pressure balance in tanks with minimal leaks and reduced emissions. This, in turn, protects valuable product and helps facility owners optimize process efficiency while minimizing downtime.
With properly chosen, installed, and maintained explosion-proof valves, hazardous-area operators can drastically reduce the likelihood of ignition events, simultaneously meeting strict safety standards and sustaining smooth, cost-effective production.
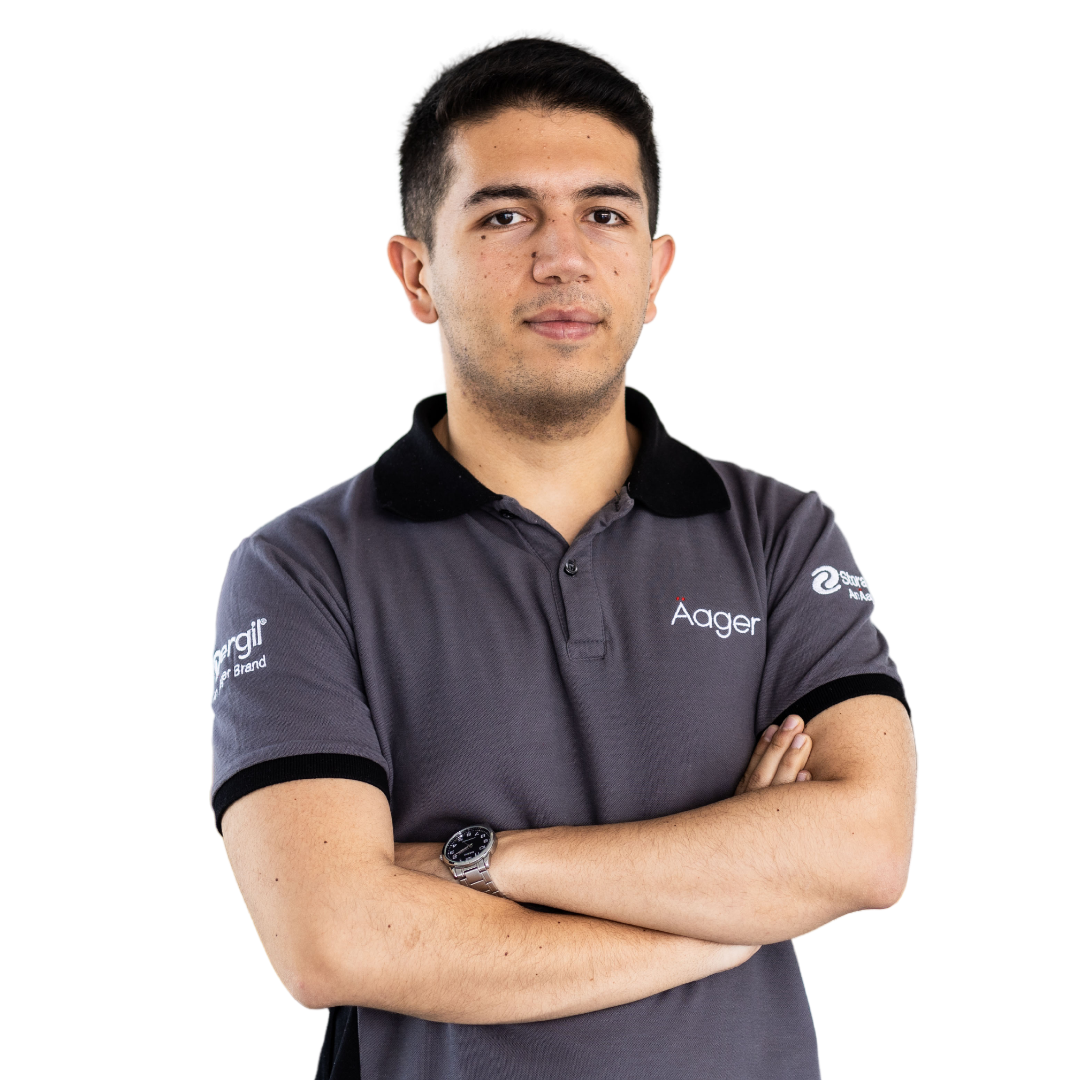
Barış KARAKUZULU
Sales Engineer
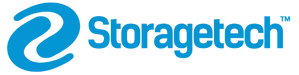