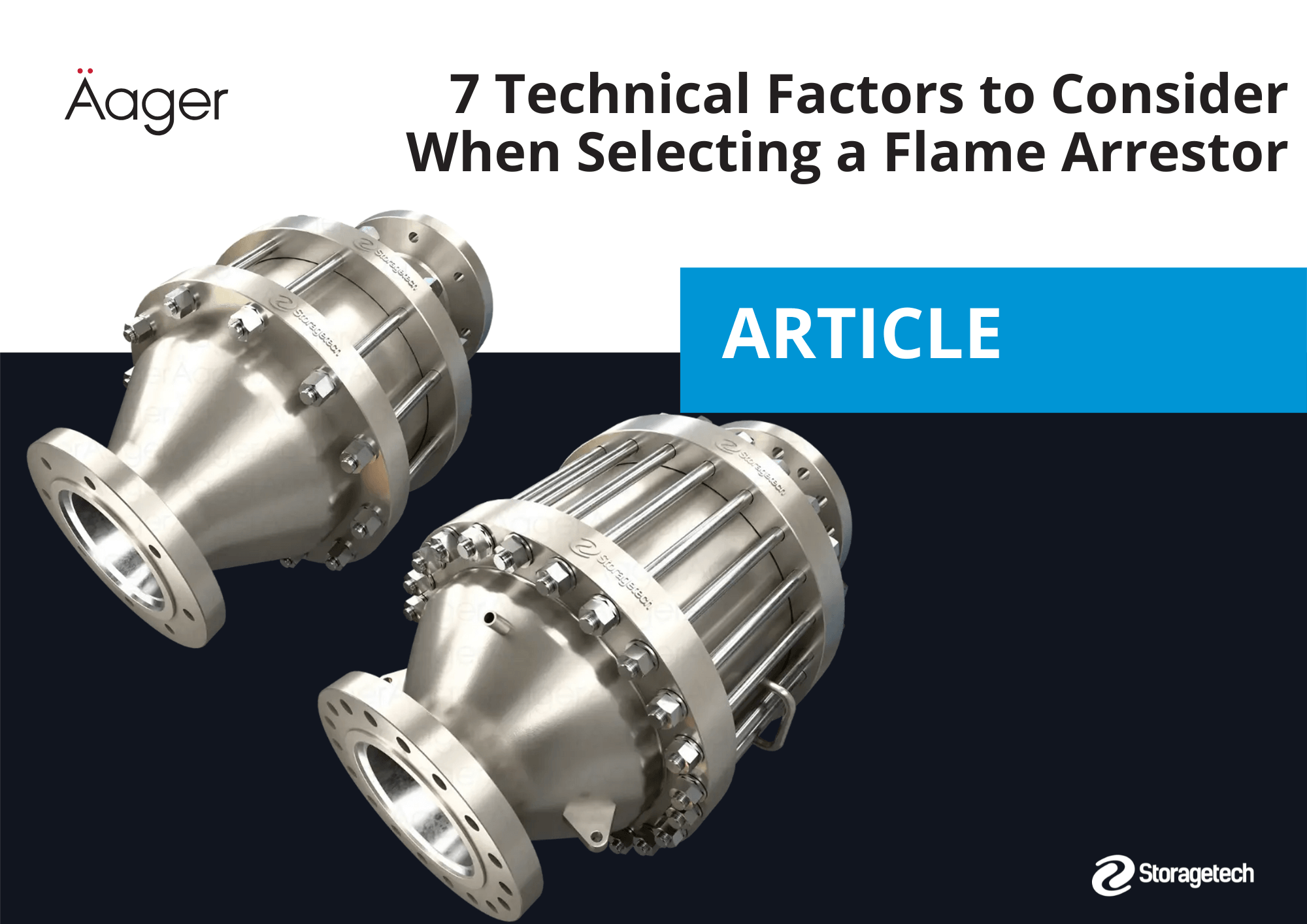
From the oil and gas sector to chemical plants and any facility handling flammable gases and vapors, flame arrestors play a critical role in both regulatory compliance and operational safety. These devices are designed to prevent a flame or explosion from propagating throughout a system—potentially saving lives, equipment, and significant capital. However, no two processes are exactly alike, and each one comes with its own unique risks and requirements. Below are 7 key technical factors to keep in mind when selecting a flame arrestor for your operation.
1. Suitability for Operating Conditions
Before choosing a flame arrestor, you must thoroughly analyze the operating conditions in which it will be used. What is the process’s working pressure, temperature range, and type of gas or vapor?
- Temperature: High-temperature processes require flame arrestors made from materials and designs that can withstand those temperatures without losing performance.
- Pressure: Pressure levels can vary significantly across different process units. Flame arrestors are tested and certified for specific pressure ranges; thus, the device must align with your system’s operating pressure.
- Gas or Vapor Type: The flammability characteristics (LEL, UEL, flash point, etc.) of different gases or vapors directly affect flame arrestor design. Some substances have faster flame speeds or lower ignition temperatures.
Pro Tip:
A comprehensive risk assessment of your operating conditions—looking beyond just nominal values to peak or upset conditions—is the first and most crucial step in selecting the right flame arrestor.
2. Pressure and Temperature Limits
Pressure and temperature are among the most influential parameters for flame arrestor performance and durability. Manufacturers typically specify the maximum operating pressure and temperature a device can handle:
High Pressure: Rapid pressure spikes (such as “pressure surges” or “shock waves” in process lines) can place extreme stress on the arrestor’s housing and internal elements.
High Temperature: Elevated temperatures can affect the mechanical properties of metals and increase the likelihood of ignition. Metal alloys used in flame arrestors must retain their integrity under these conditions.
Pro Tip:
Account not only for normal operating pressures and temperatures but also for any worst-case scenarios. Your flame arrestor must perform reliably even in extreme conditions.
3. Flow Rate and Velocity
The flow rate (or gas velocity) through the flame arrestor is another critical design factor:
Pressure Drop: A flame arrestor’s internal mesh or plate structures create resistance to gas flow, causing a pressure drop. As flow rate increases, pressure drop becomes more significant, which can affect both process efficiency and safety.
Critical Flow Velocity: A flame front travels at certain speeds. If the flow velocity in your system is exceptionally high, a flame arrestor that isn’t designed for such conditions may fail to quench the flame effectively.
Pro Tip:
When reviewing product literature or test data, make sure to check the flow capacity and pressure drop specifications. If necessary, consider larger or higher-capacity flame arrestors to ensure both safety and process efficiency.
4. Explosion Type (Deflagration vs. Detonation)
Flame arrestors are generally classified to handle deflagrations (subsonic flame speeds) or detonations (supersonic flame speeds):
Deflagration Flame Arrestor
Designed for lower flame speeds (subsonic).
Commonly used in storage tank vents, standard process lines, and low-pressure systems where the flame speed is expected to remain relatively low.
Detonation Flame Arrestor
Built to handle high-speed, supersonic flame fronts accompanied by extreme pressure spikes or shock waves.
Essential in large refinery or petrochemical operations where there is a possibility that a deflagration could transition into a detonation.
Features a more robust, complex internal structure to withstand higher pressures and mechanical shock.
Pro Tip:
Carefully analyze whether there is any chance that a deflagration could transition into a detonation in your process. If so, a detonation flame arrestor is mandatory. Using a deflagration-only arrestor in a high-risk area could leave your system vulnerable.
5. Material Selection and Corrosion Resistance
Proper material selection is paramount for a flame arrestor to function effectively. Most arrestors are constructed from stainless steel, cast iron, or specialized alloys. Key considerations include:
High Thermal Conductivity: The metal must dissipate heat quickly to quench the flame.
Corrosion Resistance: Depending on your gas or vapor chemistry, the metal must resist corrosion or chemical reactions. For instance, acidic or sulfur-rich streams may require high-grade stainless steel or specially coated alloys.
Mechanical Strength: The chosen material should withstand pressure fluctuations, temperature spikes, and potential vibrations without warping or cracking.
Pro Tip:
Conduct a thorough analysis of the chemical composition of your gas streams. For processes with high sulfur content (e.g., H₂S) or acidic properties, corrosion is a serious concern. Selecting the right material can save you significant maintenance costs and extend the device’s operational life.
6. Ease of Installation and Maintenance
Flame arrestors require regular cleaning and inspection to remain effective. Therefore, installation and maintenance considerations are essential:
Ease of Disassembly: Complex or hard-to-remove designs drive up maintenance costs and complicate shutdown schedules.
Spare Parts Availability: Common brands or widely used models typically have spare parts readily available, crucial for quick turnaround in emergencies.
Configuration Options: Flange sizes, connection types, and mounting orientations should match your system’s design. Incompatible connections can impair performance or complicate installation.
Pro Tip:
If long-term operating costs are a priority, look for flame arrestors with user-friendly access for cleaning and inspection. Also, investigate the manufacturer’s customer support and service network before making a final purchase decision.
7. Standard Compliance and Certification
For safety equipment, standard compliance is not just a formality—it is a key indicator of the product’s quality and performance. Some of the most recognized standards and certifications for flame arrestors include:
API (American Petroleum Institute): Widely referenced in the oil and gas industry.
NFPA (National Fire Protection Association) 69: Covers explosion prevention systems and flame arrestors.
ISO Standards: Define various testing and performance parameters for safety devices.
CE, ATEX, FM, UL, TÜV Certifications: These verify compliance with safety, quality, and explosive atmosphere requirements.
Pro Tip:
Always review the test reports and certification documents provided by the manufacturer. Ensure that the flame arrestor’s certification matches the explosive group (e.g., IIA, IIB, IIC) and temperature class (T1–T6) relevant to your process environment.
Mohammed HASSAN
Technical Coordinator
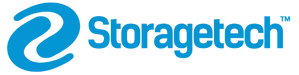