Combustion Process and Its Implications for Flame Arrestor/Arrester Technology
The combustion process is a fundamental consideration in the design and application of flame arrestors, also known as flame arresters. These critical safety devices rely on a deep understanding of combustion dynamics to effectively prevent flame propagation in potentially explosive environments. To fully appreciate the role of flame arrestors in industrial safety, it’s essential to examine the intricacies of the combustion process and how they inform flame arrester technology.
At its core, combustion is an exothermic chemical reaction between a fuel and an oxidizer. In most industrial contexts relevant to flame arrestor applications, the fuel is typically a hydrocarbon gas or vapor, while the oxidizer is usually atmospheric oxygen.
The combustion process can be broadly categorized into four main stages: pre-ignition, ignition, propagation, and termination.
The pre-ignition stage involves the mixing of fuel and oxidizer to form a combustible mixture. This stage is crucial in understanding the effectiveness of flame arrestors, as the device must be capable of handling various fuel-air ratios. The mixing process can occur in two primary ways: premixed combustion, where the fuel and oxidizer are mixed before reaching the combustion zone, and diffusion combustion, where mixing occurs at the reaction zone. Flame arresters must be designed to address both scenarios, as industrial processes can involve either or both types of mixing.
Ignition marks the beginning of the combustion reaction and can be initiated by various sources such as sparks, hot surfaces, or existing flames. The ignition energy required varies depending on the fuel type and mixture composition. This variability is a key consideration in flame arrestor design, as the device must be capable of quenching flames across a range of ignition scenarios.
Once ignition occurs, the flame begins to propagate through the combustible mixture. This propagation stage is where flame arrestors play their most critical role. The speed at which a flame front moves is a crucial parameter in flame arrester design. Laminar flame speeds, which occur in steady, non-turbulent conditions, are typically lower and easier to manage. However, in many industrial scenarios, turbulent flame speeds are more common and can be significantly higher, posing greater challenges for flame arrestor effectiveness.
Flame propagation involves complex chemical kinetics and heat transfer processes. As the flame front advances, it preheats the unburned mixture ahead of it, creating a self-sustaining reaction. This preheating is accomplished through various heat transfer mechanisms:
- Conduction: Heat transfer through direct contact between molecules
- Convection: Heat transfer through the movement of hot gases
- Radiation: Heat transfer through electromagnetic waves
Flame arrestors exploit these heat transfer mechanisms to quench the flame. By providing a large surface area for heat dissipation, typically through narrow channels or porous media, flame arresters can remove heat from the combustion zone faster than it is generated, thereby extinguishing the flame.
The combustion process is governed by several key parameters that directly influence flame arrestor design:
- Flammability Limits: These define the range of fuel-air mixtures that can sustain combustion. The Lower Flammability Limit (LFL) and Upper Flammability Limit (UFL) are critical in determining the conditions under which a flame arrestor must be effective.
- Maximum Experimental Safe Gap (MESG): This represents the maximum gap width through which a flame cannot propagate under specified test conditions. MESG is a crucial factor in determining the appropriate flame arrester for different gas groups.
- Quenching Distance: The minimum distance between parallel plates that will extinguish a flame. This parameter is fundamental to the design of flame arrester elements.
- Auto-ignition Temperature: The lowest temperature at which a substance will spontaneously ignite without an external ignition source. This is particularly important for flame arresters in high-temperature applications.
- Flame Temperature: The temperature reached during combustion, which can vary significantly depending on the fuel and combustion conditions. Flame arresters must be constructed of materials capable of withstanding these temperatures.
The combustion process can lead to two primary types of flame propagation:
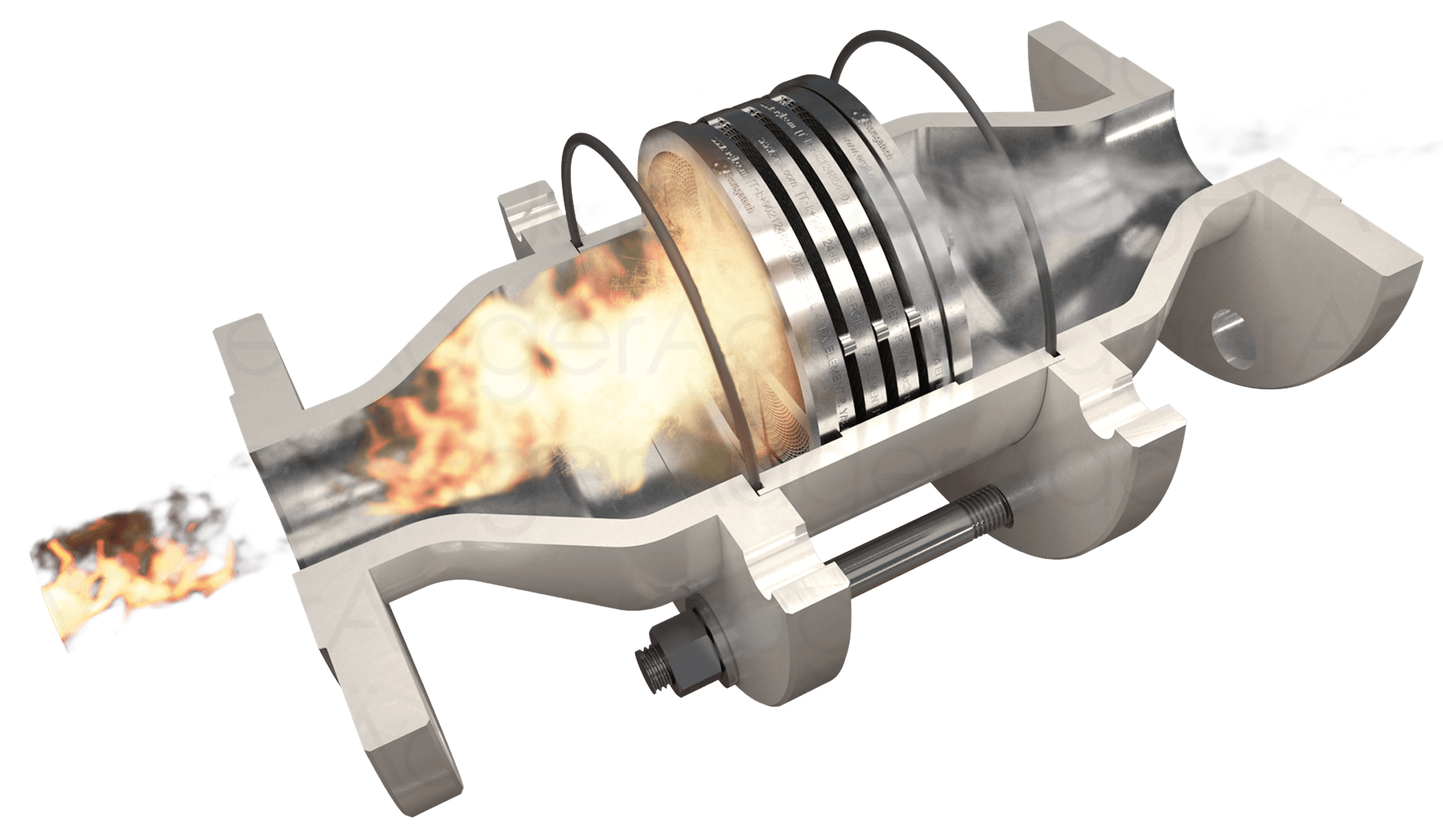
Deflagration involves subsonic flame speeds and is characterized by a flame front that moves through the unburned mixture by heat transfer and diffusion.
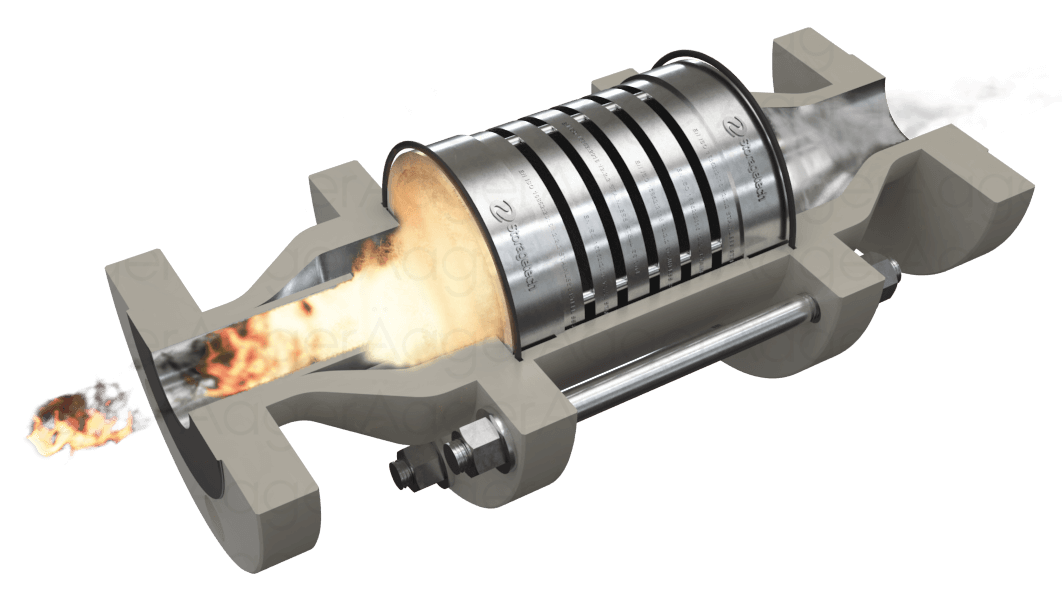
Detonation, on the other hand, involves supersonic flame speeds and is characterized by a shock wave coupled with the reaction zone.
Flame arrestors must be designed to handle both deflagration and detonation scenarios. Deflagration arresters typically use smaller gap sizes and longer flame channels to quench the flame, while detonation arresters require more robust construction to withstand the higher pressures and temperatures associated with detonation waves.
The effectiveness of a flame arrester in quenching combustion depends on its ability to interfere with the chain reactions that sustain the flame. These chain reactions involve the production and consumption of highly reactive intermediate species, such as free radicals. By providing a large surface area for these radicals to recombine, flame arresters can effectively break the chain reaction and extinguish the flame.
Flame arrestor technology must also consider the potential for accelerated flame speeds in long pipes or in the presence of obstacles. As a flame propagates through a confined space, it can create turbulence that increases the flame speed. This acceleration can potentially lead to a transition from deflagration to detonation, known as Deflagration to Detonation Transition (DDT). Flame arresters designed for deflagration may not be sufficient to stop a detonation, highlighting the importance of proper device selection based on a thorough risk assessment.
The combustion process in real-world scenarios is often more complex than idealized models suggest. Factors such as fuel composition variability, the presence of inert gases, and varying environmental conditions can all impact combustion characteristics. Flame arrestor designs must be robust enough to handle these variations while maintaining effectiveness.
Advanced computational fluid dynamics (CFD) modeling and simulation techniques have become invaluable tools in understanding the complex interactions between combustion processes and flame arrester designs. These tools allow engineers to visualize flame propagation through arrestor elements and optimize designs for maximum effectiveness across a range of combustion scenarios.
Emerging technologies in combustion science continue to inform flame arrestor development. For instance, research into nanoscale combustion phenomena is providing insights into more efficient heat transfer mechanisms that could lead to more compact and effective flame arrester designs. Similarly, advancements in materials science are enabling the development of flame arresters capable of withstanding more extreme temperatures and corrosive environments.
The ongoing evolution of industrial processes and the introduction of new fuels, such as hydrogen in the growing “hydrogen economy,” present new challenges for flame arrestor technology. These developments necessitate continuous research and development to ensure that flame arresters remain effective in an ever-changing industrial landscape.
In conclusion, a deep understanding of the combustion process is fundamental to the design, selection, and application of flame arrestors and flame arresters. By leveraging knowledge of combustion dynamics, from the molecular level of chain reactions to the macroscale behavior of flame propagation, engineers can develop increasingly effective flame arrester technologies. This ongoing pursuit of improved safety through advanced flame arrestor design is crucial in mitigating the risks associated with combustible gases and vapors in industrial settings.